Plastic injection molding process
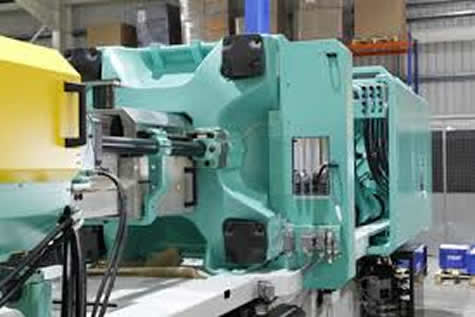
The injection molding process of plastic parts mainly includes four stages, which is filling, holding pressure, cooling and demoulding. These four stages directly determine the molding quality of products, and the four stages are a complete continuous process.
1. Filling stage
High speed filling
When filling at a high speed, the shear rate is high, and the viscosity of the plastic will decrease due to shear thinning, which will reduce overall flow resistance. The local viscous heating effect will also thin the curing layer thickness. Therefore, in the flow control stage, the filling behavior often depends on the volume to be filled. That is to say, in the flow control stage, due to high-speed filling, the shear thinning effect of melt is often very large, while the cooling effect of thin wall is not obvious, so the effect of rate prevails.
Low speed filling
When low speed filling controlled by heat conduction, the shear rate is low, the local viscosity is high, and the flow resistance is large. Due to the slow rate of hot plastic replenishment, the flow is slow, so that the heat conduction effect is more obvious, the heat is quickly taken away by the cold wall. With a small amount of viscous heating, the curing layer is thicker, these further increase the flow resistance at the thinner part of the wall.
2. Pressure holding stage
In the stage of pressure holding, due to the high pressure, the plastic exhibits partial compressibility. In the area with high pressure, the plastic is relatively dense and with high density. In the area with low pressure, the plastic is loose and with low density, so the density distribution changes with position and time. In the process of pressure holding, the plastic flow rate is very low, and no longer plays a leading role; Pressure is the main factor affecting the holding process. During the holding process, the plastic has filled the mold cavity, and the gradually curing melt acts as a medium to transfer pressure. The pressure in the mold cavity is transferred to the surface of the mold wall by the help of plastics, and there is a tendency to open the mold. Therefore, an appropriate clamping force is required for the clamping. Under normal circumstance, the rising mold force will slightly open the mold, which is helpful for the mold exhaust. But if the mold force is too large, it is easy to cause the flash, overflow, or even open the mold. Therefore, in the choice of injection molding machine, we should choose the one with enough clamping force to effectively carry out pressure holding.
3. Cooling stage
Cooling system design is very important in injection mold. This is because the molding of plastic products only cooling and curing to a certain rigidity, it can avoid deformation after demolding due to external force. Because the cooling time accounts for about 70% ~ 80% of the whole molding cycle, a well-designed cooling system can greatly shorten the molding time, improve injection molding productivity and reduce costs. Improper cooling system will prolong the molding time and increase the cost. Uneven cooling will cause warping and deformation of plastic products.
The factors affecting the cooling rate of products:
Plastic product design
Mold material and cooling method
Cooling water pipe configuration
Coolant flow
Property of the coolant
Plastic selection
Processing parameter setting
4. Demoulding stage
Demoulding is the last step in an injection molding cycle. Although products have been cold molding,but demoulding still has a very important impact on the quality of products. Improper demoulding may lead to uneven force in demoulding and deformation of the product during ejection. There are two main ways of demoulding: ejector rod demoulding and stripper demoulding. In order to ensure the quality of the products, we should choose the proper demoulding method according to the structural characteristics of the products.
For the ejector rod demoulding, the ejector rod should be set as uniform as possible, and the location should be selected in the place where with the maximum demolding resistance and maximum strength and stiffness of the plastic parts, to avoid plastic deformation.
For stripper demoulding, it is generally used for deep cavity thin-wall containers and transparent products without the trace of push rod. This kind of mechanism is characterized by large and even demoulding force, smooth movement and no obvious traces left behind.
If you are looking for a product or a moulder, please visit our website:http://www.china-plasticmolding.com and contact us.